Nemo enim ipsam voluptatem quia voluptas sit aspernatur aut odit aut fugit, sed quia conse quuntur magni dolores eos quit.
Industrial Partner
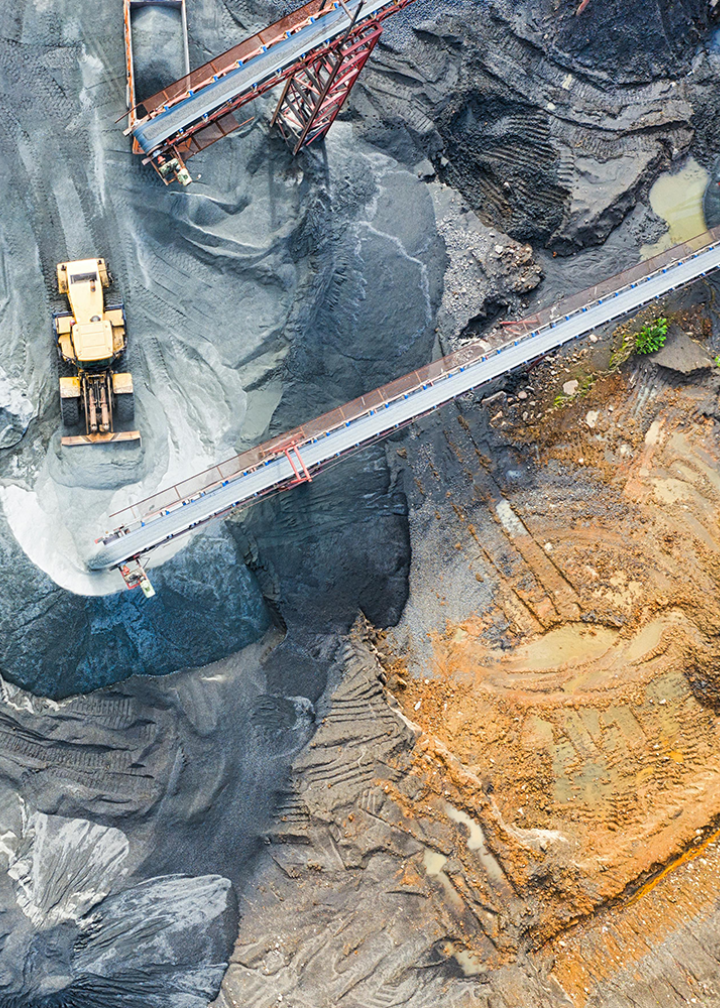
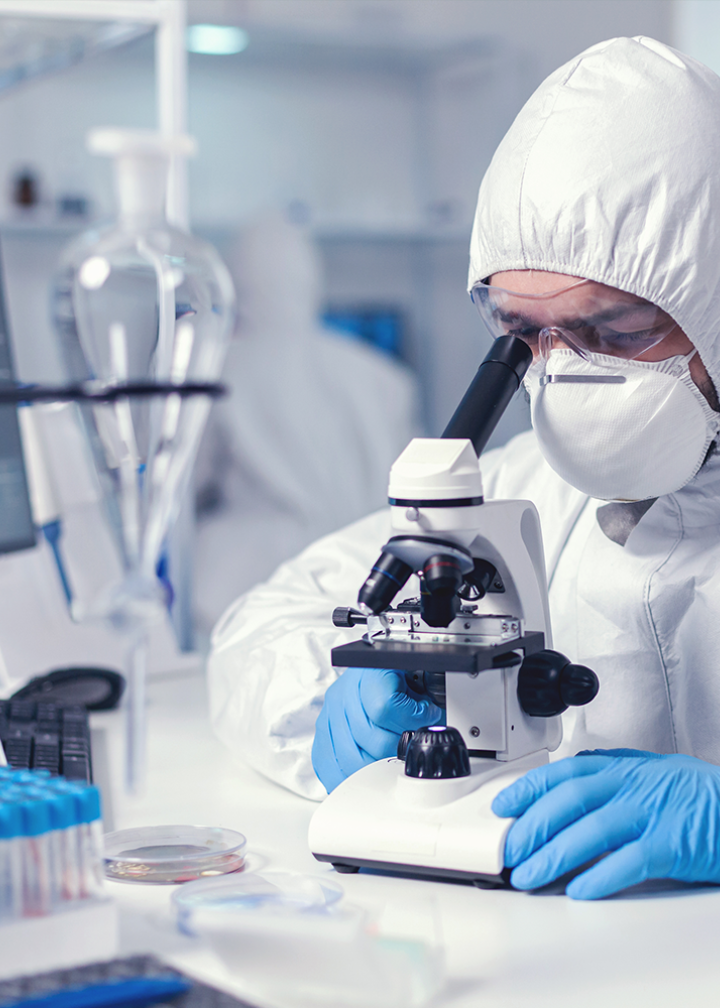
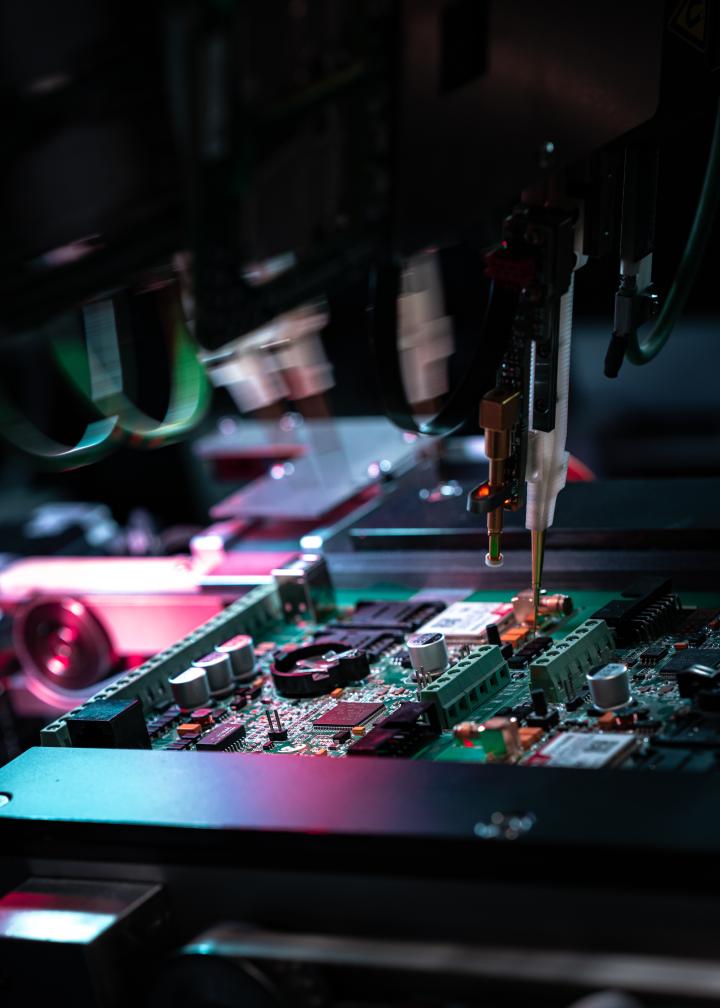
Les processus de transformation multimatériaux et multitechnologies conçus par nos équipes s’adaptent aux exigences spécifiques de chaque industrie, quel que soit son domaine d’activité. Grâce à notre force de développement, notre expertise de transformation et notre compréhension reconnue du monde industriel, nous garantissons la création de pièces qui rencontrent les besoins de nos clients en matière de qualité, durabilité et efficience pour contribuer à leur avantage concurrentiel.
Moins d’eau pour des composants de douche
L'enjeu
Depuis plus de 25 ans, Devillé group fabrique des pièces techniques par injection plastique pour un acteur majeur de la robinetterie française. Celui-ci équipe de grands stades dans le monde comme le stade vélodrome de Marseille, le parc des Princes de Paris, le Camp Nou de Barcelone pour n’en citer que quelques-uns. On le retrouve également dans d’autres grands domaines tels que l’hôtellerie, l’enseignement, le commerce, le plein air, etc…
Le défi
Notre client travaille chaque jour pour économiser une ressource qui devient rare : l’eau. Il est donc primordial pour lui de concevoir des produits qui optimiseront sa consommation. Afin de l’accompagner dans ce challenge et développer de nouvelles pièces ou composants en plastiques, les équipes de Devillé group n’ont pas hésité à plonger dans son univers.
Notre réponse
Le pôle développement de Devillé group a récemment travaillé en co-conception sur un support de colonne de douche. Cette dernière, initialement fabriquée en aluminium puis usinée et assemblée, est maintenant composée à 90 % de plastique technique avec une charge importante en fibres de verre pour conserver les caractéristiques mécaniques.
Tout le savoir-faire de Devillé group en injection de matière plastique technique a permis de répondre à l’ensemble des problématiques de notre client. Ce travail de co-conception a finalement confirmé la nécessité de conserver un insert métallique pour sécuriser la fixation du produit. Les simulations numériques (études rhéologiques) ont permis de valider en avant-projet le design et la robustesse de la pièce avant de lancer la réalisation de l’outillage définitif.
Les moyens
Pour suite de cette étape de de faisabilité, nos équipes projet ont développé un outillage de surmoulage, ainsi que le process d’industrialisation sur îlot robotisé pour le chargement automatique de l’insert dans le moule. Cette production permettra d’approvisionner les lignes d’assemblage de notre client pour les 20 prochaines années.
Les bénéfices
-
100% des caractéristiques mécaniques maintenues avec le changement de technologie
Les suites
Le produit final est donc toujours aussi robuste mais également plus économique grâce à une gamme de fabrication plus courte.
Une solution innovante née de la collaboration étroite entre nos équipes et celles de notre client. Une belle réussite qui ouvre bien d’autres perspectives car le catalogue de notre client contient de nombreuses pièces qui pourraient bénéficier de ces évolutions technologiques.