EN : Nemo enim ipsam voluptatem quia voluptas sit aspernatur aut odit aut fugit, sed quia conse quuntur magni dolores eos quit.
Industrial Partner
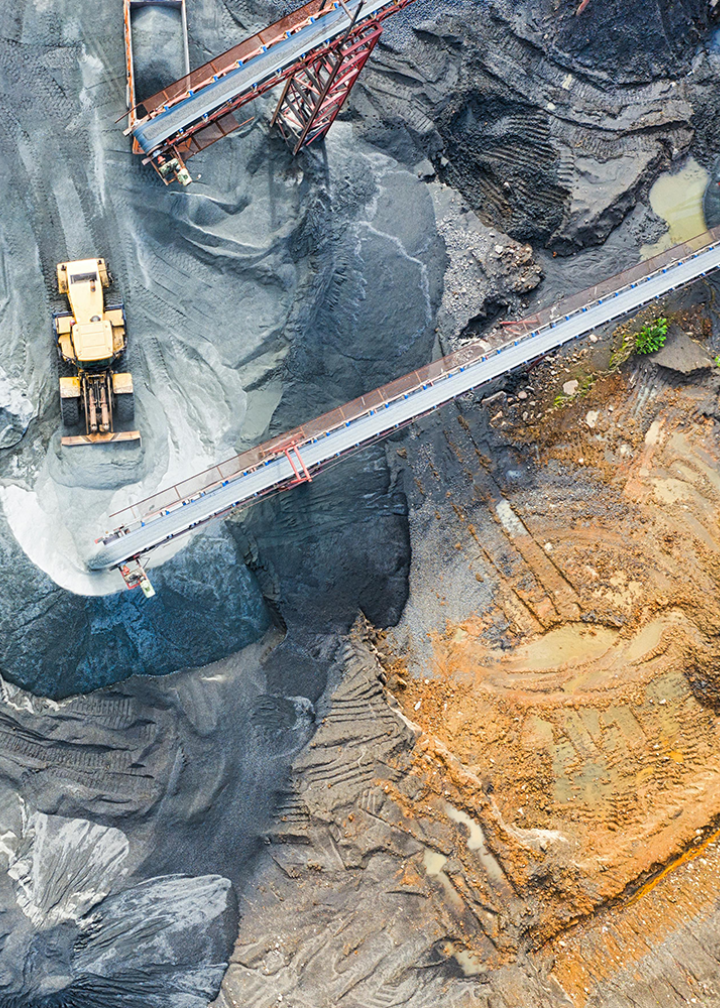
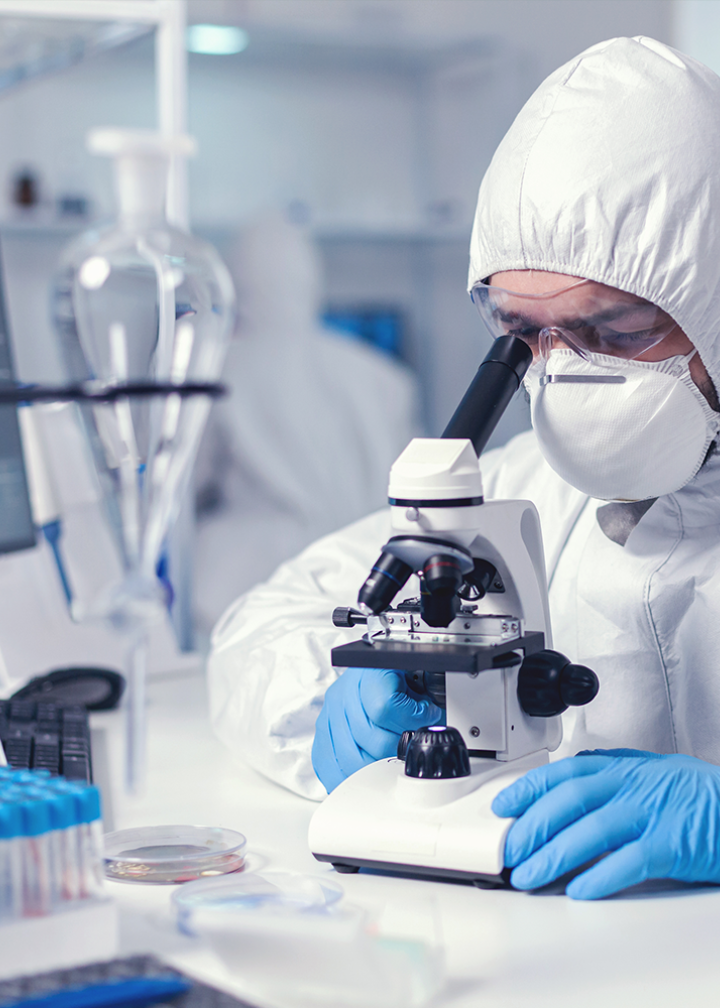
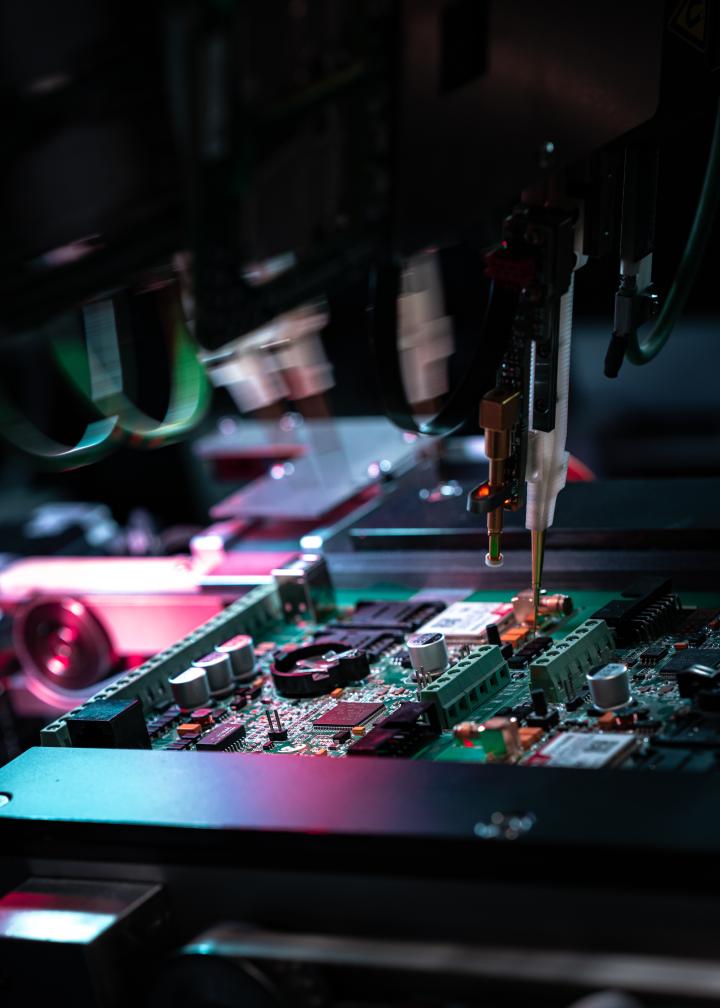
The multi-material and multi-technology transformation processes designed by our teams adapt to the specific requirements of each industry, regardless of its field of activity. Thanks to our development strength, our processing expertise and our recognized understanding of the industrial world, we guarantee the creation of parts that meet our customers' needs in terms of quality, durability and efficiency to contribute to their competitive advantage.
Less water for shower components
The issue
For over 25 years, Devillé Group has been manufacturing engineered parts using injection moulding for a major French tapware company. Our customer fits out big stadiums around the world including the Marseille velodrome, Parc des Princes in Paris and Camp Nou in Barcelona. They also operate in other big sectors such as hospitality, education, retail and outdoor facilities.
The challenge
Our client works daily to conserve a dwindling resource: water. It is therefore essential for them to design products that optimize consumption. To support them in this challenge and develop new plastic parts or components, Devillé's teams did not hesitate to dive into that world.
Our response
Devillé Group's development department recently worked in co-design on a shower column support. Initially made of aluminum, machined, and assembled, it is now composed of 90% technical plastic with a significant fiberglass load to maintain mechanical characteristics.
The means
Devillé Group's development department recently worked in co-design on a shower column support. Initially made of aluminum, machined, and assembled, it is now composed of 90% technical plastic with a significant fiberglass load to maintain mechanical characteristics. All of Devillé Group's expertise in technical plastic material injection has responded to all of our client's challenges. This co-design work ultimately confirmed the need to retain a metal insert to secure the product's fastening. Numerical simulations (rheological studies) validated the design and robustness of the part in the pre-project phase before proceeding with the final tooling manufacturing.
The benefits
-
100% of mechanical characteristics preserved despite the change in technology
Future directions
An innovative solution born from the close collaboration between our teams and those of our client. A great success that opens up many other possibilities because our client's catalog contains numerous parts that could benefit from these technological advancements.