EN : Nemo enim ipsam voluptatem quia voluptas sit aspernatur aut odit aut fugit, sed quia conse quuntur magni dolores eos quit.
Mobility Industries
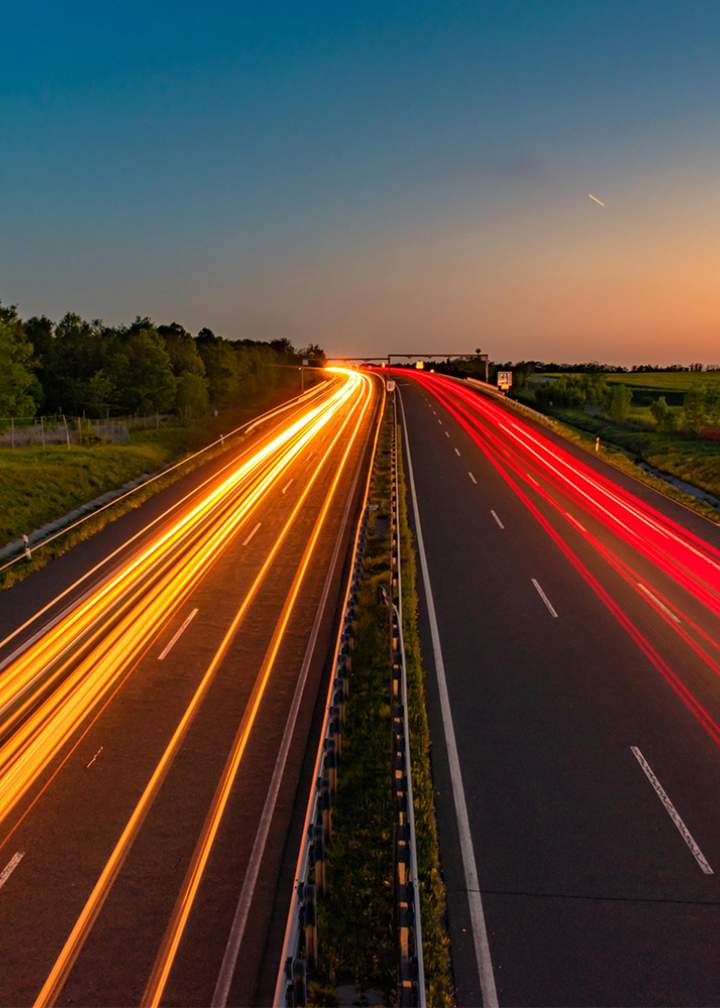
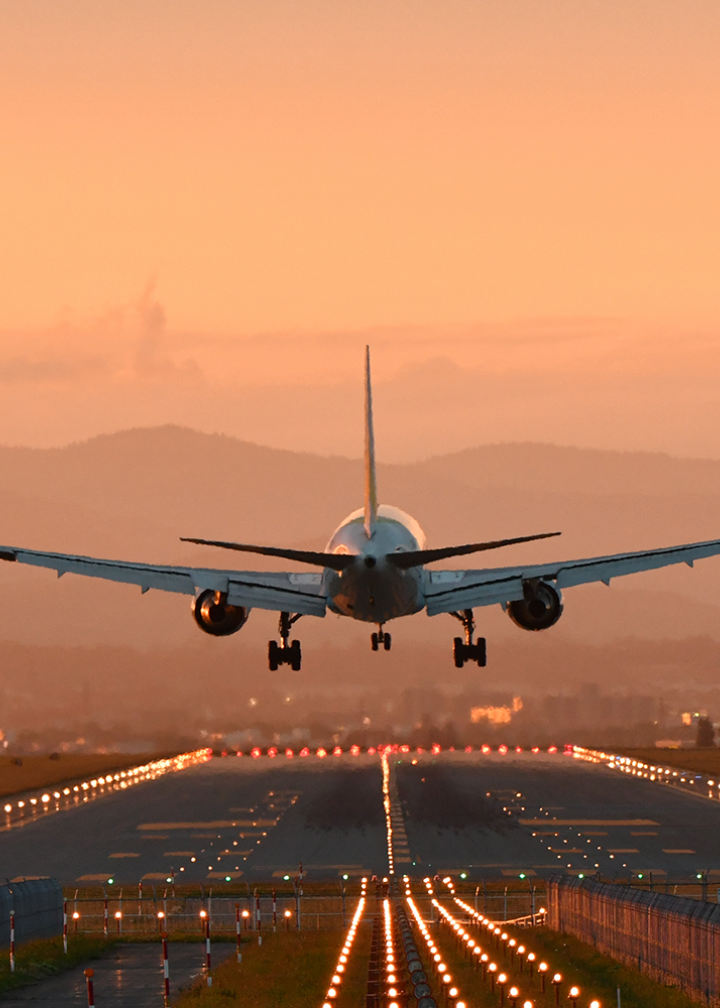
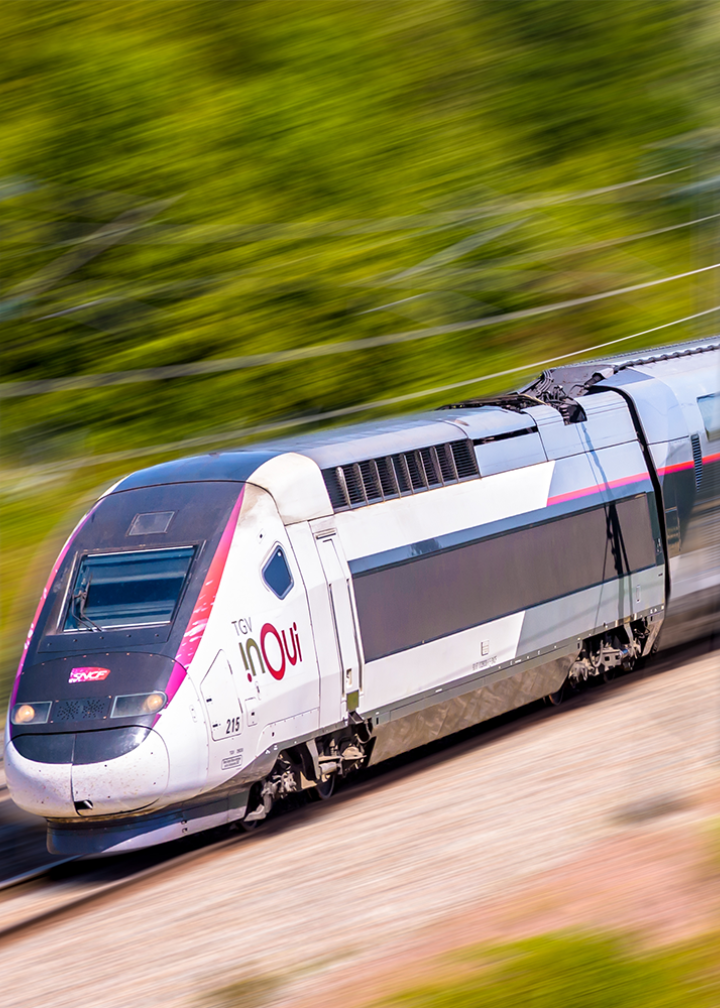
We are proud to count among our customers big names in the mobility industries (automotive, trucks, lifting, etc.). These fruitful partnerships are a testament to our ability to design tailor-made solutions that meet their performance and transformation challenges - electrification, hydrogen, connectivity, sustainability - and to produce industrial components of excellence.
The challenge of safety belt anchors
The issue
Environmental concerns and electrification are encouraging vehicle manufacturers to reduce raw material consumption and the weight of their vehicles. To achieve those goals, they must consider every component... Even down to the seat belt anchor plates (which attach the seat belt strap to the vehicle’s chassis).
The challenge
Environmental concerns and the shift toward electrification are prompting automotive manufacturers to reduce vehicle weight and raw material consumption. To achieve these objectives, every component must be considered... even the safety belt anchors (which secure the belt webbing to the vehicle chassis). Devillé Group typically produced these parts in the tens of millions using a high strength steel stamping process. However, a new design proposed by our clients allowed for a nearly 25% reduction in thickness (while maintaining safety standards). How could we industrialize and standardize production for this new design?
Our response
Devillé Group has been addressing weight reduction challenges for over 20 years—long before the current electrification trends. To meet this new challenge, we have developed a new technological solution : forming with a rolling-edge cutting tool (known as "rolling edge"), using steel that's 10 to 15% stronger than the previous version.
The Means
We carried out the first stages of development in partnership with research centers in Poland and Angers, adjacent to our industrial sites. Prototype tools and simulations helped define optimal shapes for cold-forming a steel bead on the fittings (which protects the integrity of the safety belt webbing when it rubs against the anchor). This co-development effort led to defining a standard industrial forming process, closer to cold forming than traditional stamping methods. Devillé Group’s tooling experts then developed tool preparation solutions. In partnership with our suppliers, we selected the most efficient materials and appropriate surface treatments to ensure optimal tool life. Our methods and quality teams also developed control measures and production equipment maintenance systems to ensure consistent quality and safety standards over the years and millions of parts produced.
The benefits
- -25% less steel consumption to perform the function
- +25% more durable component in crash situations
Future directions
As often happens, one advancement leads to another. Studying materials and their forming theory has provided insights into the metallurgy of steels' impacts on production processes, as well as the effects of punch/die settings on the integrity of all safety parts already in serial production. For over 20 years now, Devillé Group's metal factories have been producing this new design of anchors and are ready to tackle new challenges in the rational use of raw materials in the industry.